GeoSeals
Real-time stock alerts on emergency nutrition supplies, from any health distribution point, anywhere.
To save lives, humanitarian aid needs to be in the right place at the right time.
GeoSeals provides early warnings on stock outs of emergency nutritional supplies in health distribution clinics serving some of the world's most vulnerable communities.
Seeking to provide humanitarian distributors with a more transparent overview of stock whereabouts, our technology gives real-time data on the locations of emergency nutritional supplies as they move through the supply chain.
Watch the 15 minute film
We would love your support to amplify this story.
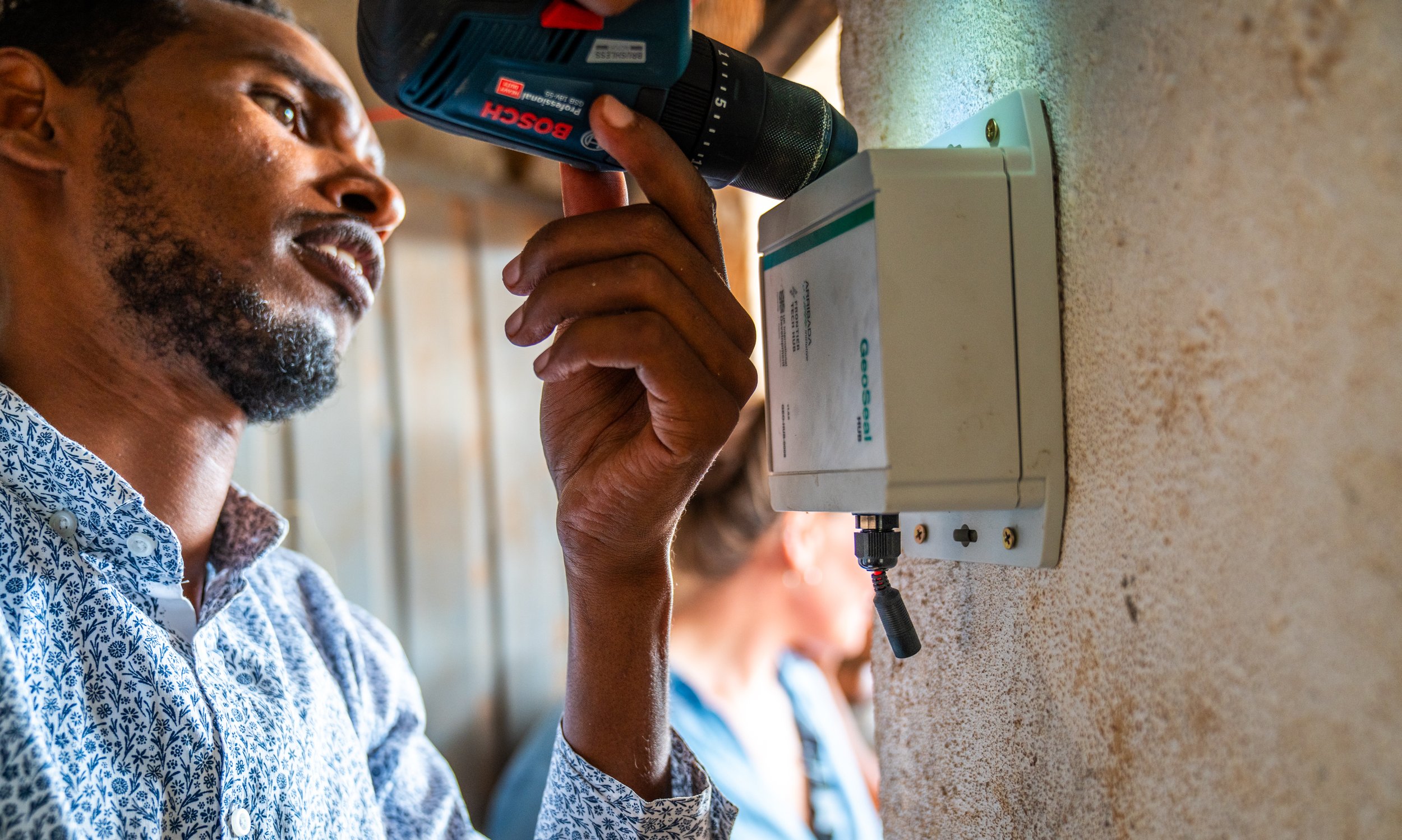
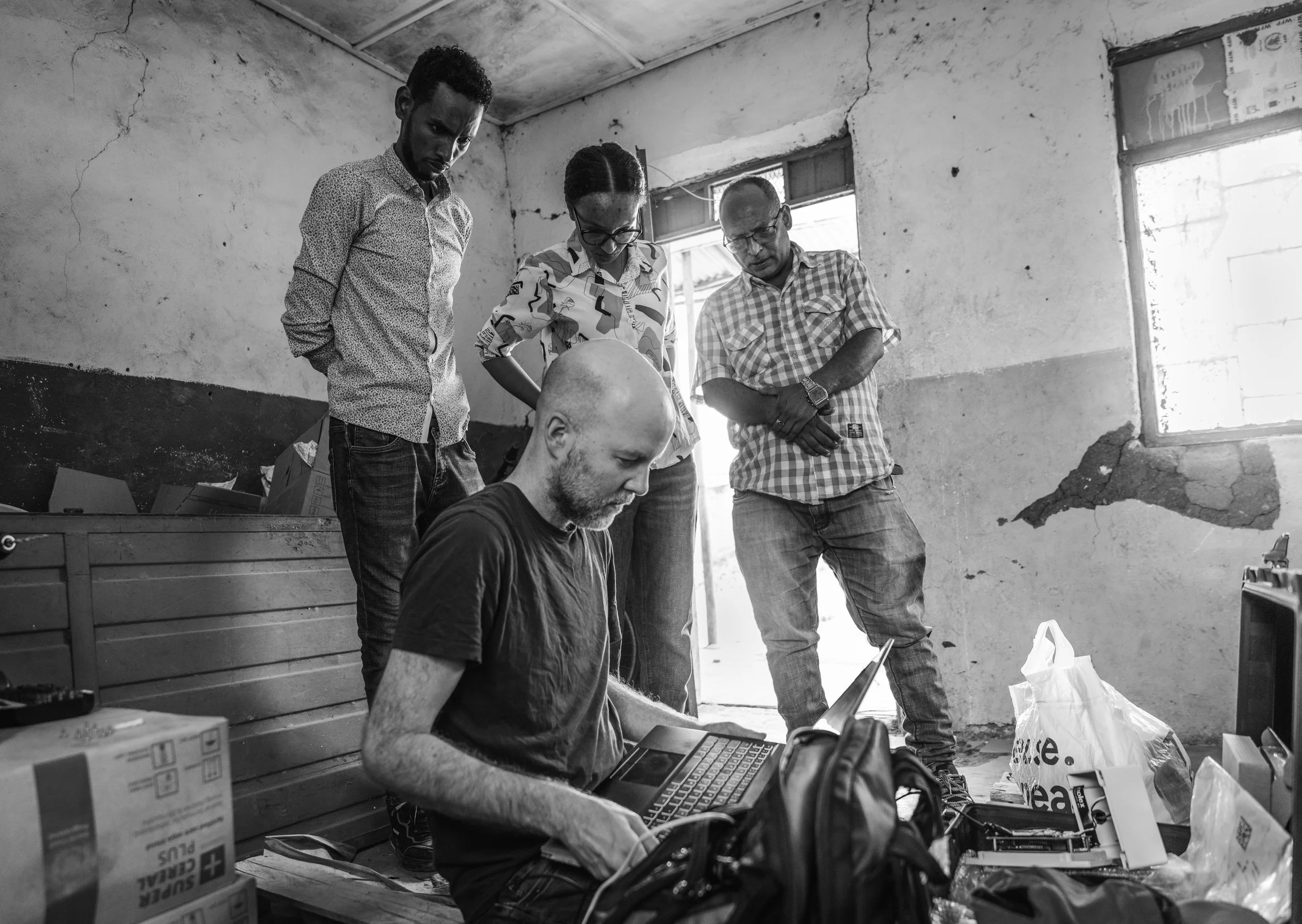
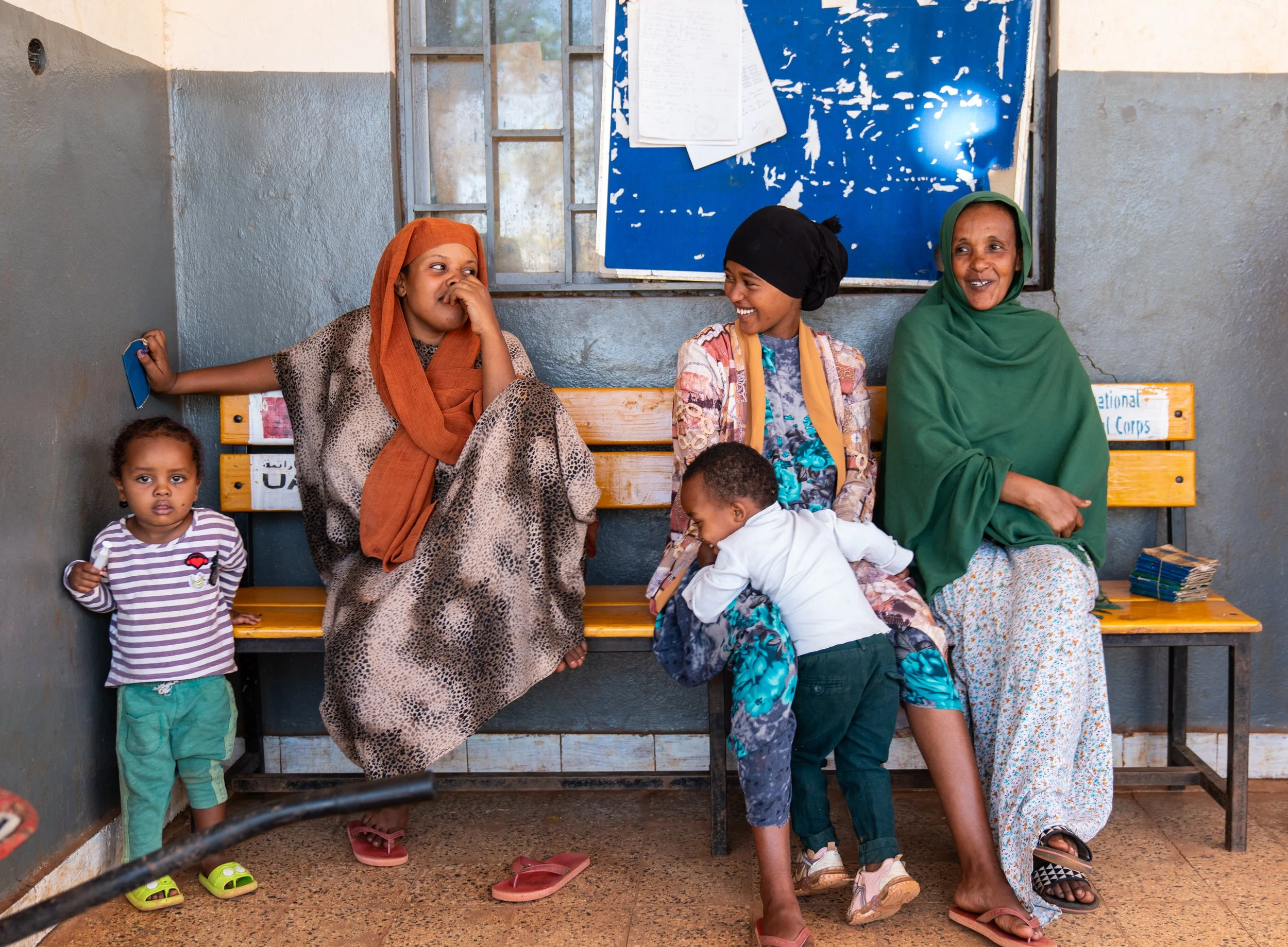
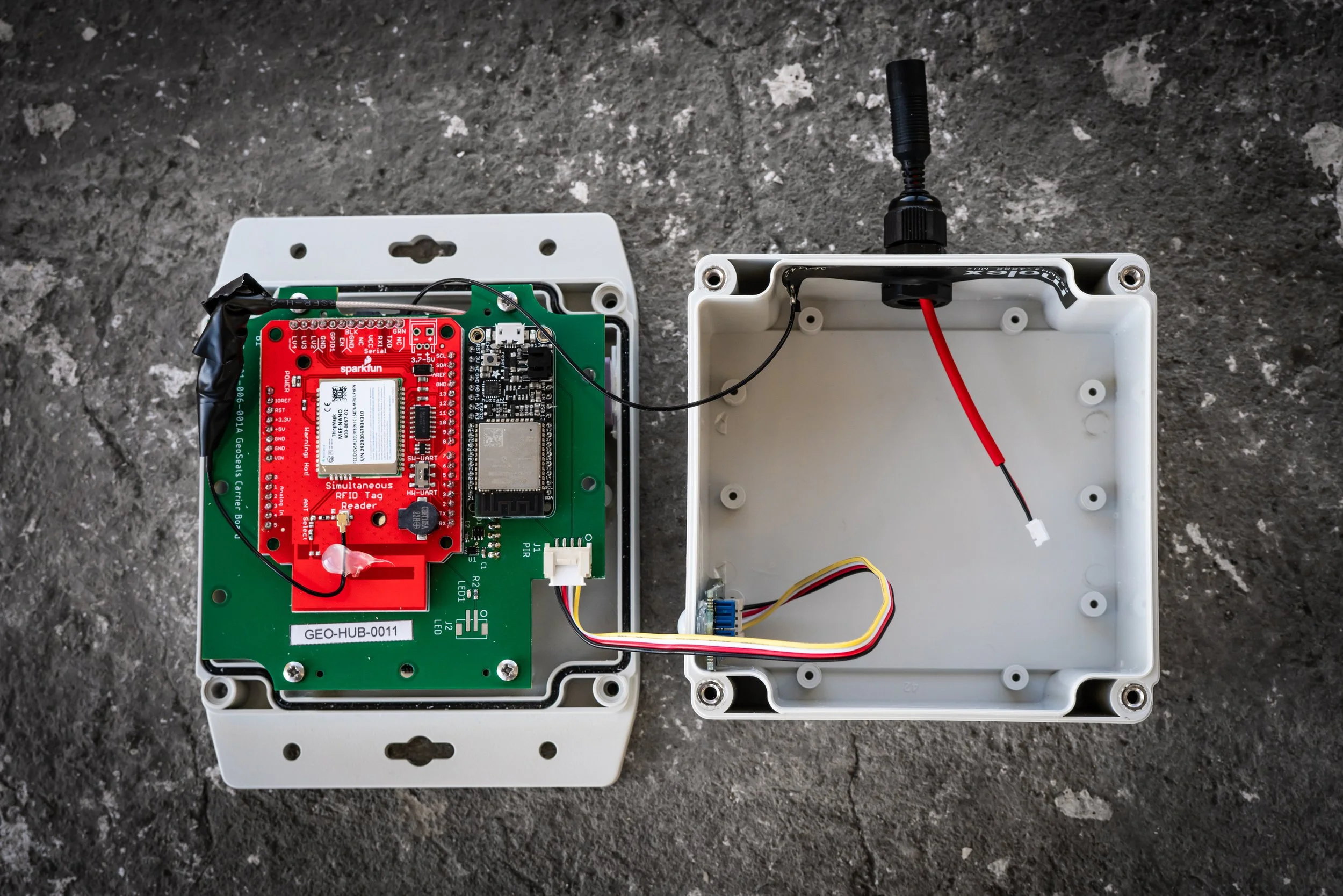
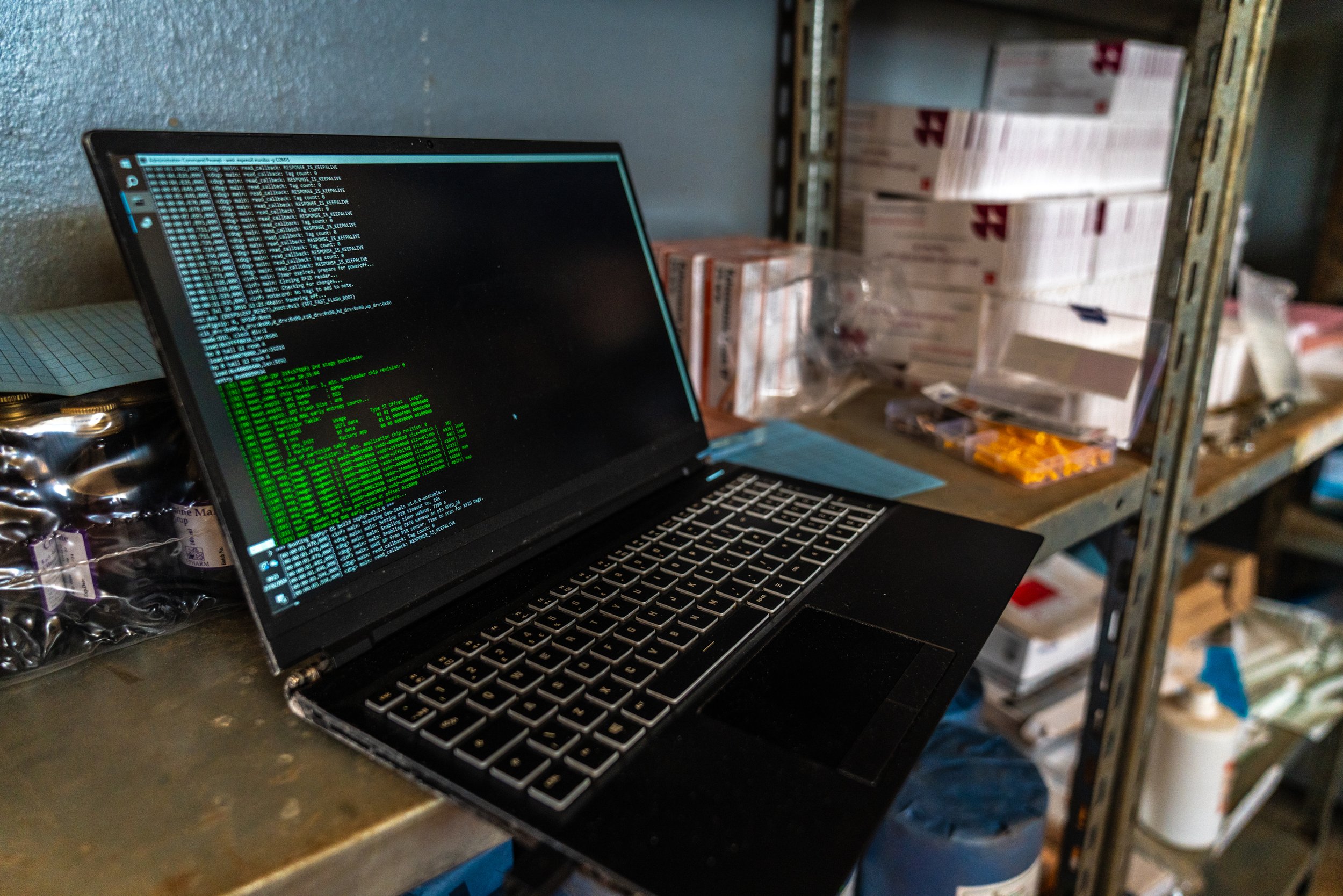

In hard to reach conflict zones, areas without electric and internet connectivity and where staff are overstretched, reliable real time data does not exist. This results in stock running out, medicines expiring and inefficiencies in delivery. Ultimately this puts the lives of the most vulnerable on the line.
The anticipated outcome of the GeoSeals product is data: reliable, automated monitoring of stock levels at clinics and a clear understanding of where and when supplies are being used. This data could be used by aid agencies and governments to ensure that clinics are stocked.
The initial trial took place in March this year, with an attempt to track RUTF (ready to use therapeutic food) to rural health points in Harar, Ethiopia. They installed GeoHubs at 6 distribution points, enabling them to track 200 boxes of RUTF supplies. There are 24,000 distribution points in the RUTF supply chain in total.
Further more, RUTF is one of the hardest aid commodities to track because of its high water content. So if this trial works, the possibilities for impact across the sector seem endless.
Questions and answers
During our event in October 2024, the GeoSeals surfaced questions from attendees from across the government, philanthropy and charity sectors. You can watch a recording of the event here.
Please see answers to the questions below*
*Please scroll down for a glossary of terms used.
-
It was a proof of concept trial. The best indicator of our success was the visualisation shared in our presentation, which shows that we were able to use our fleet of hubs to produce data that traced the entire journey of a single box of RUTF nutritional supplies throughout its supply chain run. Since this was a proof of concept, it really was about finding out if tracking the journey of a box of nutritional supplies was even possible.
-
The GeoHubs that we installed in Ethiopia for the proof of concept trial only have cellular connectivity. Our next hub design, which we are working on now, will also have satellite capability, which our GeoHubs will use as a second-resort option for when cellular connectivity is interrupted, or extremely weak. Additionally, our GeoHubs will also store the data locally (on the device itself).
-
The GeoHubs that we used for the proof of concept trial were made from off-the-shelf components, which obviously adds expense, so they currently cost £400 to make. We hope that by early 2025 we will have halved this cost. Each RFID tag costs 10p.
-
This question refers to this initiative. We have no alignment with this strategy but are very pleased that it exists! We are aware of the potential that GeoSeals technology has for transporting other emergency humanitarian supplies, not just nutritional ones. In fact, RUTF and RUSF, known as ‘Plumpy Nut’ , is actually the hardest consumable to track, because of the density of the peanut butter. The good news is that once we crack tracking this, there are many other humanitarian consumables that will be much easier to apply our technology to, including medical supplies.
-
Not yet, but who knows what the future holds… The weight and sheer volume of boxes moving through the supply chain would make this tricky (and therefore expensive), but it’s a nice idea.
-
Our data would be shared with our partners, for example UNICEF and WFP, in the form of a dashboard. The data would be confidential and used only by designated personnel within these organisations.
The question around visualisations is an interesting one which we’re working on at the moment; it all depends on who the users are within the organisations, that is, whether they are monitoring stock outs, or are, for example, more interested in analysing supply chain flow. Since our data is geospatial, it’s likely that the initial view of the data will be map-based. We expect to also incorporate time series graphs which show the deliveries of stock into individual HDPs, perhaps plotting this against consumption rates. Sankey diagrams are also a great way to show supply chains, and heat maps are a useful indicator of stock levels across an ecosystem of last mile HDPs. There are lots of possibilities, and it’s all about taking our partners’ KPIs and combining them with our data to give the most intuitive picture of what is happening.
-
Arribada is a conservation technology company, and we’re only just moving into the humanitarian sector. So in that regard, we’ve learnt a great deal about how the development sector works, and have enjoyed working with new partners such as WFP, UNICEF and the FCDO.
In any healthy project, there are always pivots along the way. An example of when we had to rethink our approach was, when designing the technology originally, we assumed that boxes would be carried into storage facilities individually, with both hands, carried in front of the body. Actually, in the field, we realised that boxes are often carried on the shoulder, which makes the boxes a little harder to detect. So we had to rethink things a little after that observation. But such discoveries are how you make progress, and they are exactly what Human Centred Design is about, an approach championed by our engineer Ruby.
-
The phase of funding that we’re currently in is all about us producing that ‘playbook,’ that is, knowing what funding and resources we would need to install and run a network of 100 hubs in Ethiopia, to then build this into a larger ecosystem. Even now, we are very interested in trialling our technology in other locations in Africa and beyond, as it helps us to develop a product that is versatile in the locations and situations that it can be useful, and in the commodities that it can track.
-
It took several months to design the hub, but one can be assembled in about a day. Obviously these figures are not relevant to our plans to eventually mass produce the hubs. Our hubs would most likely be mass produced here in the UK. We would love to build our hubs in Ethiopia but sadly the cost this would incur in sourcing components and factories, not to mention different standards in manufacturing quality, mean that it would not be feasible.
-
We did extensive research into existing logistical solutions prior to designing our technology and defining the project. To paint a picture, most of the heath distribution points (HDPs) which are at the end of the supply chain are in areas with very little cellular coverage, and no source of power. So conventional logistics solutions were not suitable. Our entire approach for the design of the technology is based around these factors, hence our use of a solar panel and battery system, and an infrared sensor as the trigger for the hub to complete a scan, because this method saves a great deal of power.
-
Both UNICEF and WFP have existing systems. We see this as another tool that can be used in their existing systems. One aspect that makes GeoSeals unique is that it works without the need for human intervention - no need to take/send photos or to scan barcodes etc. The costs of GeoSeals are also very low compared to a barcode scanning system that is currently used in some large warehouses in Ethiopia.
-
It has been important to gain ownership from all the main stakeholders incl. Govt of Ethiopia (Ministry of Health senior management and clinic staff etc.), UNICEF, WFP, FCDO Ethiopia. To do this we kept circling to the big picture problem that everyone wanted to solve i.e. reducing malnutrition in Ethiopia. We then listened to what the individual stakeholder needs were. To build engagement we were clear that we were not arriving with a solution but wanting to work together to co-create.
-
A comprehensive coverage of warehouse network and health centres would provide detailed data on stock progressing through the stock chain. It would reveal any anomalies and unexpected patterns. We do think that this will be useful in addressing aid diversion. I thought https://healthsites.io/ would have warehouses in it, but sadly not!
-
GeoSeals are currently applied at the box level. Each truckload will have a number of pallets, each pallet a number of boxes. We don't tag at the individual sachet level as this would not be practical or cost effective.
Extensive research was carried out into how packaging, and indeed re-packaging, happens along the RUTF supply chain. When designing the technology, Alasdair and Ruby carefully considered where the best point along the supply chain would be to tag the boxes, knowing that in order to be successful, GeoSeals needed to be easy to incorporate into existing supply chain processes. -
Data is only securely available internally. Our data system and the dashboard that we create for organisations such as UNICEF and WFP would only be used by designated users in these NGOs. More generally, considering security risks such as the one you point out is an integral part of designing our data system and ensuring that data security systems are of the highest standards.
-
We used RFID tags instead of barcodes. This choice was made to make implementation into the supply chain easier, and for cost reasons.
The GS1 Standard mentioned is explained here: https://www.gs1us.org/industries-and-insights/standards
-
Apple AirTags rely upon a network of bluetooth devices in close proximity to one another, so this option would be extremely expensive to implement.
-
For the problem we are solving, there are no market-based options already available. Arribada is highly experienced in delivering technology designed to survive in all sorts of extreme locations, be that the rainforest, the Arctic, the ocean… The lack of market-based options was exactly the reason that Arribada was drafted in for this project; we are good at creating bespoke technology solutions.
-
This is certainly a variable that we would love to incorporate into the GeoSeals service. Initially, our approach is to refine the technology that we have and deliver the data insights we’re already proposing, because we want to get this perfect first. Then we will work to add additional data items such as expiry dates.
-
We were asked to address the issue of stockouts by our partners at the FCDO prior to the pilot, so our technology was born out of this request.
Our proof of concept trial was intended to show that the tracking of consumables across the supply chain in Ethiopia was possible (and we showed that it was!). We are not currently providing data on stock outs. We are in the phase where we determine how we will install GeoHubs in 100 locations in Ethiopia, which will happen in early 2025. This will be the stage where we start producing stock out data.
-
This is an excellent question, and yes we have. We are currently in talks with the Met Office, ESRI and the FCDO to think about what severe weather events would most directly affect UNICEF and WFP supply chain systems. Great point!
-
Labels are manually stuck to the boxes before entering the supply chain. As GeoSeals are in sticker form, this process takes seconds, with minimal disruption to the existing supply chain.
-
Given the strength of the adhesive this is unlikely, but of course possible. In reality, if this was to cause our system’s ‘loss’ of one box, as a proportion of the boxes flowing through the supply chain, this is not a concern.
Glossary:
HDPs - Health Distribution Points (storage facilities for emergency nutritional supplies, many of which are situated in very isolated rural villages, where there is no electricity).
RUTF - Ready to Use Therapeutic Food (used to treat severe wasting in children)
RUSF - Ready to Use Supplementary Food (used to treat moderate acute malnutrition)
RFID - Radio Frequency Identification (a wireless system that uses radio waves to identify and track objects; functions a little bit like a barcode)
Follow GeoSeals on LinkedIn to keep up with their journey as they work towards their goal to install 100 GeoHubs across Ethiopia in partnership with WFP and UNICEF.
Read the report for our pilot 'Smart GeoSeals to track delivery of humanitarian aid' here